On the Road: MABA executive director tours more plants in the region
WSSC Water Piscataway & New Bioenergy Facility and Lancaster Area Sewer Authority Facility
As you might recall, MABA’s recently appointed executive director, Mary Firestone, joined MABA Board members earlier this year for her first tours of facilities in the region including Capital Region Water of Harrisburg, Pennsylvania and Derry Township of Hershey, Pennsylvania. The first tours aided Mary in beginning to understand the world of wastewater treatment and biosolids, and she was eager to begin planning future tours to afford an even better grasp of the biosolids sector.
“It’s one thing to speak about the ideas and treatment processes, but I’ve always found myself to be much more of a hands-on learner,” she said, “Being able to see the facilities and watch it as it happens really brought it all together.”
And that understanding grew more still, as Mary and MABA Board members Anne Marek and John Uzupis, toured the WSSC Water Piscataway and construction for the new Bioenergy Facilities, as well as the Lancaster Area Sewer Authority in April. Malcolm Taylor, Principal Environmental Engineer for WSSC Water provided Mary with a complete tour of the current Piscataway facility as well as the construction process on the Bioenergy Facility, and Ed Lyle, Operations Chief, and Brian Wilcox, Plant Operations Director provided Mary, John, and Anne with a tour of the Lancaster Area Sewer Authority.
The Lancaster Area Sewer Authority (or LASA) currently owns, operates, and maintains a sanitary sewer system that serves approximately 40,000 customers representing about 125,000 citizens and 1,400 businesses located in nine Lancaster County municipalities.
“I read with interest about Mary’s recent tours, and reached out to offer a tour of our facility in Lancaster County,” said Mike Kyle, Executive Director of LASA. “We have a 15 MGD treatment plant with newly installed sludge handling that includes anaerobic digesters, an indirect sludge dryer, and covered storage.”
WSSC Water is transforming the way the Piscataway Water Resource Recovery Facility will handle waste from five existing water resource recovery facilities. The Piscataway Bioenergy Project - the largest and most technically advanced project ever constructed by WSSC Water - will use innovative technology to recover resources and produce green energy.
“Since the Piscataway WRRF is at the same location of the site of our Bioenergy Plant construction, I thought it would be a good opportunity for Mary to see what we are doing now and give her an idea of what we will be transitioning to,” said Malcolm Taylor, “The Piscataway Bioenergy Project will transform how WSSC Water handles biosolids, and is expected to lower operating costs by $3 million per year while reducing greenhouse gas emissions by 15%.”
The MABA Board and the executive director are eager to continue the plant tours in the coming months. If you are interested in sharing your facility with Mary and the MABA Board, please contact her at [email protected], or 845-901-7905. |
|
SPOTLIGHT on COMPOST
Composting is an enduring process for transforming biosolids into a Class A EQ product. Compost facilities in the mid-Atlantic region span a full array of sizes, technologies, and ownership models. The region has facilities located both at small water reclamation plants and at large treatment plants. It has windrow systems, enclosed static pile, and in-vessel agitated beds. Composting is done with various amendments -- purchased wood chips, yard debris, and organic matter recovered from solid waste. The region has various ownerships -- municipally-owned and operated composting, municipally-owned and contract-operated, and privately-owned merchant facilities. The common element to all of this variety is a product that is has a firm place in the landscape market for use in residential and commercial landscaping, as a component in soil blending, and as a specialty amendment for agriculture. Biosolids compost is a well-tested and well-accepted soil product. What is more, at least two more biosolids composting facilities are in permitting within the region. Below are several of the branded biosolids compost products made by MABA members
McGill SoilBuilder Premium Compost
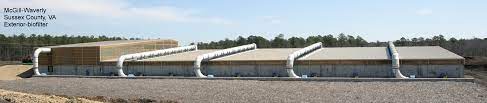 For more than 30 years, McGill Environmental Systems has designed, built, and operated state-of-the-art indoor facilities for industrial-scale production of McGill SoilBuilder Premium Compost. It manufactures this premium compost product through the processing and recycling of non-hazardous, biodegradable by-products and residuals from municipal, industrial, and agribusiness sources. The McGill Regional Composting Facility at Waverly (McGill-Waverly) opened in 2008. It is in Sussex County, Virginia, near the town of Waverly. Its primary service area includes the coastal mid-Atlantic region. This encompasses the District of Columbia south through Richmond-Tidewater to northeastern North Carolina. McGill-Waverly accepts all types of biodegradable materials including food waste and compostable plastics. It is designed to receive and process source-separated wastes transported in roll-off containers, tractor-trailer rigs, and other commercial vehicles that can safely tip into the receiving bunker. Located on a former timber tract, the operation processes in both banked and encapsulated bays with aerated curing. Aerated curing eliminates the need for windrow turners at this facility.
For more information, contact Sean Fallon, Business Development Manager, [email protected], 919-406-4270. The Waverly facility is located at 5056 Beef Steak Rd, Waverly, VA 23890.
WeCare Compost
WeCare Denali, a division of Denali Water Technologies, operates 24 composting facilities around the United States, two of which are county-owned biosolids composting plants. The Burlington Biosolids Composting Facility is a 300 ton per day capacity composting facility in Columbus, NJ, owned by Burlington County, but operated by WeCare Denali, serving about 20 agencies in the county and beyond. It is the largest biosolids facility in New Jersey under contract operations. The Rockland Green Co-Composting Facility, owned by the Rockland County Solid Waste Authority, recycles biosolids from wastewater plants in Rockland County, NY. At both plants, biosolids are mixed with clean wood waste and then composted in in-vessel agitated bed composting systems. The finished product is used on golf courses, flower gardens, and landscaping projects, and are also ingredients in topsoil This plant is adjacent to the Authority's Materials Recovery Facility and Transfer Station in Hillburn, NY. WeCare Denali markets a suite of WeCare Compost products under its WeCare Compost, Mulch, & Soil line.
For more information, contact national sales manager, Ryan J. Cerrato, [email protected], 315-575-4595. The Burlington facility address is 800 Coc-co Lane, PO Box 318, Columbus, NJ 08022. The Rockland facility is 1988420 Torne Valley Road, Hillburn, NY 10931.
ORGRO High Organic Compost
ORGRO is a product of the Baltimore City Compost Facility, a facility owned and operated by Veolia, under contract with the city of Baltimore Department of Public Works. This facility, which was first built in 1984, processes a 45 dry ton per day portion of the anaerobically digested biosolids from the Back River Wastewater Treatment Plant, the balance made into a thermally dried product. The compost plant produces about 35,000 cubic yards of compost in through in vessel composting and extended curing. This facility is one of the original national examples of a public-private partnership, and one of the original programs for commercial marketing of biosolids to commercial landscapers.
For more information, contact Tom Fantom, project manager, [email protected], 410-354-1636. The facility address is 5800 Quarantine Road, Baltimore, MD, 21266.
Landscaper’s Advantage
Landscaper’s Advantage is the product of the A&M Compost Facility, a large enclosed static pile composting plant owned and operated in Manheim, Pennsylvania by the J.P. Mascaro company. It is a merchant plant, accepting biosolids from a wide reach of plants in the mid-Atlantic. The facility is nearly 15 acres under roof. Its website offers a “ virtual tour” slide deck describing the components of its operation and its environmental controls, which includes under one cover both aerated composting and biofiltration. A&M is managed by a registered professional engineer, Ryan Inch, PE, and a compost specialist, Mark Hubbard.
For more information, contact Matt Mascaro, [email protected], 267-228-5288. The facility is located at 2022 Mountain Rd, Manheim, PA 17545.
earthlife Compost
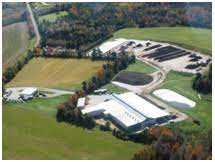 The Hawk Ridge Composting Facility, New England’s largest compost facility, is owned and operated by Casella Organics, a MABA Board member This facility uses an in-vessel tunnel system (the Gicom Tunnel) to compost a blend of biosolids with woodchips and sawdust, producing a screened compost with the tradename earthlIfe. Recently, Hawk Ridge reached the distinction of delivering its one-millionth cubic yard of compost. Its wholesale customers include golf courses, nurseries, garden centers, and athletic facilities.
For more information, contact John Leslie, [email protected], 207-461-1000. The facility is located at 3 Reynolds Road, Unity, ME 04988. |
|