July 2025 - MABA Biosolids Spotlight
Provided to MABA members by Bill Toffey, Effluential Synergies, LLC
SPOTLIGHT on PFAS Track Down
“It is complicated.” This was the assessment offered by Linda Lee, Distinguished Professor, Agronomy Environmental & Ecological Engineering, Purdue University. On its face, the concept is simple. A principle inherent in the Clean Water Act is that pollutants interfering with the safe recycling of biosolids need control at their point of discharge to public sewers. From this principle, if PFAS in biosolids are a risk to human health and the environment, PFAS sources need to be identified, and their discharge stopped. Dr. Lee explains, “unlike addressing things like Cd and Pb, where industrial point sources could be treated, we are learning that much of the PFAS load in our influent in most cases is coming from domestic sewage and storm water.” Although industrial pretreatment has worked well in league with Part 503 National Disposal Standards, it is a strategy difficult to apply to the complicated class of 12,000 persistent organic compounds covered by the umbrella term PFAS. Dr. Lee, the “go-to” PFAS researcher for the biosolids profession, who has devoted a major part of her professional career to assessing persistent organic pollutants, is working to unknot those complications. “With EPA 40 [referring to the Method 1633 used to characterize 40 selected PFAS in biosolids and wastewater] typically less than 25% of the PFAS are captured. The actual influent is not characterized for most of the precursors of the monitored ‘EPA 40’ list, including precursors from domestic sources, landfill leachate and AFFF [aqueous firefighting foam].” How can you “track down” polluting fluorinated chemicals if you don’t know the identity, the sources and the processes that transform unmeasured “precursors” during water reclamation facilities into “monitored” biosolids-borne PFAS? That is why the concept of PFAS track down is complicated. “It is complicated,” admits Stephen Kuplicki, manager of industrial pretreatment for the Great Lakes Water Authority (GLWA). GLWA is the public owner of a 600+ MGD plant in Detroit, MI, the second largest WRRF in the U.S., and an early collaborator with the Michigan EGLE (the Department of Environment, Great Lakes, and Energy), the state environmental agency leading most other states in a response to PFAS risks. Since 2017, Kuplicki has worked with over 200 significant industrial users to “track down” industrial releases of PFAS. One avenue for simplification was EGLE’s decision to focus on one of the thousands of PFAS compounds, PFOS, as a kind of “indicator” compound that stands out in most scans of biosolids for PFAS. The track down resulted in a selection of about 50 sources with high PFOS concentrations, helpfully concentrated in such industry groups as centralized waste treatment, airports, metal coaters, and fire training facilities. Over the past 8 years, GLWA has worked with those sources to mitigate their mass loadings. Despite this huge effort, Kuplicki has concluded that most measured PFOS is from domestic sources, not regulated point sources. He has observed inexplicable spikes in effluent PFAS loadings, which may or may not be related to storm events, but may be legacy sources on lands and in sewers. He has uncovered sub-watersheds to the wastewater collection system exhibiting infiltration of PFAS-contaminated groundwater. He has seen what he suspects is break through PFAS discharges from treatment devices installed by industries. So, the most advanced WRRF effort in the U.S. to reduce PFAS influent discharges has resulted in a tenuous, complicated connection between industrial discharges of PFAS and subsequent effluent discharges. “It is complicated,” implies Joshua Balentine, Senior Manager for Client Services with Brown and Caldwell in Memphis, TN, when asked whether his clients are eager to track down PFAS at their facilities. Balentine has worked with several municipal clients in setting up industrial pretreatment programs for PFAS monitoring. “Some agencies want to get ahead of the curve by studying their PFAS sources, but the vast majority are not sampling unless required by regulators to do so.” Balentine quickly adds that in several instances state regulators put agencies in a bind by not accepting any analytical result for PFAS above non-detect for approving biosolids for land application. The risk of future restrictive state standards for PFAS in biosolids has several clients undertaking analyses as part of a master planning effort, but in most states, regulations are not yet a driver. Balentine believes that a forthcoming EPA survey of POTW influent for PFAS will encourage more state regulatory involvement in PFAS. Until then, many agencies will take a “wait-and-see” approach to PFAS monitoring, and Balentine’s encouragement of PFAS track down may be seen as too “bleeding edge.” “It is complicated,” says Dr. Scott Mansell, Division Manager of the Research and Innovation Program at Clean Water Services (Portland, OR) in characterizing the sources of PFAS to the water and soil environments, both in the Portland region and out in the farming areas. The strong leadership at Clean Water Services, holding to the principle that the reputation of its biosolids recycling program rests on trust and transparency with the PFAS issue, has had that agency complete over 1,400 samples of water, soil, and biosolids to help understand the flow of PFAS around its region. Scott is joined at CWS by a talented team, notably Operations Analyst Dr. Summer Sherman-Bertinetti, Environmental Services Specialist Amanda McGarry and Reuse and Biosolids Manager (and wetlands scientist) Jared Kinnear in the biosolids and residuals program. This team is working to understand urban streams with PFAS concentrations very nearly equal to wastewater effluent, over farms soils in the region with unexpected background PFAS concentrations, and with urban wetland sites proposed for land application of reuse water with unexpectedly high baseline PFAS levels in groundwater. From where does all that PFAS come? How can added risk of biosolids or effluent be judged against the existing ubiquity of PFAS in the urban water and soil environment? The CWS PFAS testing program is working toward instilling confidence among its client farmers and their communities that biosolids and effluent can be recycled for the nutrient and soil building qualities within bounds of acceptable risks drawing on its commitment to research and data transparency and with outreach and education. “It is complicated,” James Fotouhi, Resource Recovery Program Manager at DC Water, suggests when, having committed to a thorough track down of PFAS discharges, his agency essentially came up empty handed. Even when factoring airports and landfills into the track down, no discharger to the Blue Plains facility has a mass loading of PFAS the control of which would have any meaningful impact on PFAS in the agency’s effluent or biosolids concentrations. “We know some of our residents are concerned about PFAS, so we are exploring a public outreach program that helps our customers understand the potential sources of PFAS in the products they use every day.” While the direct use today of PFOS, the monitored PFAS target compound, for waterproofing and stain resistance has been greatly reduced over two decades, replacement fluorinated ingredients in cosmetics, fabrics and packaging remain in use, and some of these are the precursors that Dr. Lee and many others are investigating. But the development of an effective public outreach program to encourage use of PFAS-Free products is a complicated task. “It is complicated,” Molly Trembley, Environmental Engineer, Division of Materials Management at NYS Department of Environmental Conservation, says about defending the soundness of her state’s biosolids recycling program considering the political heat that scapegoats biosolids as a principal health risk. Trembley is part of an interdivisional team at NYS DEC that is looking at PFAS from the viewpoint of several residuals and from aquatic and fishery health in addition to public health and soil quality, requiring sound science to define the problem and to analyze the scope of risks. The part of the issue engaging Trembley is a survey of all biosolids generators approved in New York State for land application or composting. The generators are eager for the results, but the activists and the legislators are even more eager for results. Fending off premature legislative actions is complicated when such actions could have irreversible damage to longstanding recycling programs and when research results take time. “It is complicated, a hundred percent,” asserts Doug Daley about his survey for NYS DEC of some 90 biosolids generators in New York. Daley is Associate Professor & Director of Analytical & Technical Services at SUNY Environmental Sciences and Forestry, contracted by NYS DEC to survey and characterize PFAS in the biosolids of public WRRFs. He has encountered nothing but positive cooperation among treatment facilities, but, that said, all sampling must adhere to impeccable standards to avoid contamination, and analytical costs are expensive, upwards of $400 each. Analytical results for all facilities will be complete in September, and then the data crunch will take place, to characterize results according to plant size, geography, industrial contributors, and socioeconomic characteristics. Graduate students working with Daley have been tracking current research elsewhere on the ubiquitous sources of fluorinated compounds contributing to PFAS in sewage, including PFAS carried in the 25 kg/capita of toilet paper annually flushed to WRRFs. The research team is also seeking to frame biosolids as a PFAS source against typical concentrations in other composts and fertilizer products and in soils that have only been impacted by atmospheric deposition. “It is complicated,” Malcolm Taylor, PhD PE, Principal Engineer, Engineering & Environmental Services at WSSC Water, says of his agency’s proposal to research the fate of biosolids-borne PFAS in farm soils, crops, groundwater and surface runoff. WSSC Water has a major investment in production of a high quality biosolids product with thermal hydrolysis followed by mesophilic digestion, and public and regulatory support for its “Class A EQ Biosolids,” a product similar to DC Water’s Bloom, is critical. WSSC Water and Virginia Tech worked to craft the research protocol, responding to the interest of Virginia Department of Environmental Quality (VDEQ) to see scientifically-based data results in support of its regulatory programs. The research site is a large farm in Shenandoah Valley not previously used for biosolids, and it has been permitted by VDEQ for biosolids use and research. A multi-disciplinary team, assembled by Dr, Taylor, includes pragmatic scientists at Virginia Tech, Michigan State University and University of DC, with the field operations expertise of Synagro. Brown and Caldwell will work with this team to ensure results are assembled into an array of reports and presentations for regulators, elected officials and the community. The environmental fate of PFAS at land application sites is an emerging area of inquiry, and WSSC Water and its team may very well face unexpected complications in its ambitious research, as the study of PFAS pathways in farm soils, crops and water is complicated. “It is complicated,” explains Larry Hentz, Senior Vice President, HDR Engineering, Inc., “and it can be very expensive,” in describing installation of PFAS removal equipment to mitigate a major PFAS source in just one small community. The State of Maryland is putting up $20 million to treat a groundwater source of PFAS impacting community drinking water in Hampstead, Maryland, a town of 6,400 residents in rural Carroll County. The priority for environmental infrastructure must be treating drinking water supplies, as public water supplies can be a key pathway of human exposure to PFAS. Hentz intends to track this project, as well, for its potential to benefit PFAS mass loadings to the Hampstead wastewater treatment facility. When elevated, PFAS in drinking water may prove to be a significant source of PFAS discharged to public sewers, and its mitigation in drinking water may benefit biosolids; or maybe it will not. Again, understanding influent sources of PFAS and the point of control for mitigating those sources is complicated. “It is complicated,” John Uzupis, Technical Services Director at Synagro out of Baltimore, MD, in discussing the factors set up against the recycling of PFAS-bearing biosolids. Uzupis has been a witness to citizens who believe government and businesses cannot be trusted to act with integrity; he has seen legal actions taken as a first step rather than as a step of last resort; he sees news media more interested in easy explanations and finding evildoers than in truth and facts; he listens to politicians responding to uninformed citizen pressure rather than to professional expertise; and, he is witnessing regulators backing away from long standing policies and regulations that have supported biosolids recycling. Finding a solution to dousing the flames of unreasonable fear stoked around PFAS in biosolids is difficult when so many of past supporters of biosolids recycling seem to be stepping away, despite growing evidence that PFAS in biosolids is at most a minor issue. But federal and state funding for sound science and regulation development seems to be disappearing in today’s world, as Uzupis sees it, and that makes the challenge of operating biosolids recycling programs very complicated. Track down of PFAS sources in wastewater for the purpose of mitigating concentrations of PFAS in biosolids? Well, it is complicated. Very complicated.
For more information, contact Mary Baker at [email protected] or 845-901-7905. |
|
May 2025 - MABA Biosolids Spotlight
Provided to MABA members by Bill Toffey, Effluential Synergies, LLC
SPOTLIGHT on Young Professionals in the MABA Region
Ryan Chewinski
“I have visited a farm, looked around, and seen a slice of Heaven.” Ryan Cherwinski says this of his joy in working with the farming community to line up land application sites for biosolids. Ryan is a “relationship person,” and sees his work with the Mid-Atlantic region of Denali Water Solutions as an opportunity to provide genuine value to farmers stressed by high costs of fertilizers and by low prices for their products. He works as a regional manager in Pennsylvania and eastern Ohio. This position allows him to witness an “instant reaction” in crops and to aid the farmer’s land stewardship of his land, providing services that are of significant help. He doesn’t see himself doing anything else, as he values his relationship with the landowners and he enjoys facing new challenges every day.
After graduating Bloomfield University, Ryan moved to the Northumberland County Conservation District and then Dauphin County District, serving as an agricultural conservation technician. He has been with Denali since February 2021 and resides in Dauphin with his wife and their three-month-old daughter.
Ryan is an outdoors guy, with a love of fishing and hunting, and he is grateful for a job that allows him a lot of outdoor time.
He enjoys being of service to farmers. He tries to take off their plate the time and cost of managing nutrients, a service that includes providing spreading equipment and low-impact vertical tillage. As was the case as a Conservation District employee, he values the lasting relationships with farmers, each of whom is unique. As most of the farmers have adopted no-till cultivation practices, the customary cycle for surface application of biosolids is three years, applied to mostly field corn crops, either before planting or after harvest. This cycle allows for avoidance of excessive buildup of phosphorus. For some farms, Denali can deliver alum sludge from public water filtration systems, and the alum helps to bind up phosphorus to reduce release to the waters. Ryan has moved into this role of regional manager with the valuable support of his Denali colleagues, notably Tommy Baro for field operations and Stefan Weaver for regulatory steps.
While much of his work time has him with farmers, mine reclamation has been his favorite project. He recalls visiting a previous project site after a midwinter snowfall and witnessing a majestic herd of elk grazing the land. He has seen an abundance of turkeys, geese and mammals reoccupy lands that had been disturbed by mining in the bituminous coal region, and he is motivated by the many thousands of disturbed landscapes across the state. Where Baro and Weaver have been Ryan’s farm specialist, in mine country this advisor role is Greg Barchey’s to play. Denali deploys a portable unit for blending biosolids with lime to achieve stabilization and liming, and Barchey was a key part of the team that designed it and got regulatory approval. Portability allows the unit to be placed conveniently after mine closure activities have placed overburden over the rock. But this region has poor soils and natural soil as a final cover is scarce, so Ryan deploys large chisel plows and disc harrows to make several passes over the surface layer onto which the allowable 60 dry tons of biosolids, together with the lime amendment, have been placed. In some cases, the disturbed lands are owned by hunting clubs, and seed mixes can be tailored to landowner requests. Ryan says the results are infallibly amazing, in stark contrast to the meager growth on mine sites treated with conventional fertilizer and hydroseeding, and relationships with the mining companies are understandably strong. Ryan has developed a good working relationship with the region mining office of the Pennsylvania DEP that reviews sites for biosolids use, and attributes that relationship to the “visuals” of a strong vegetative cover.
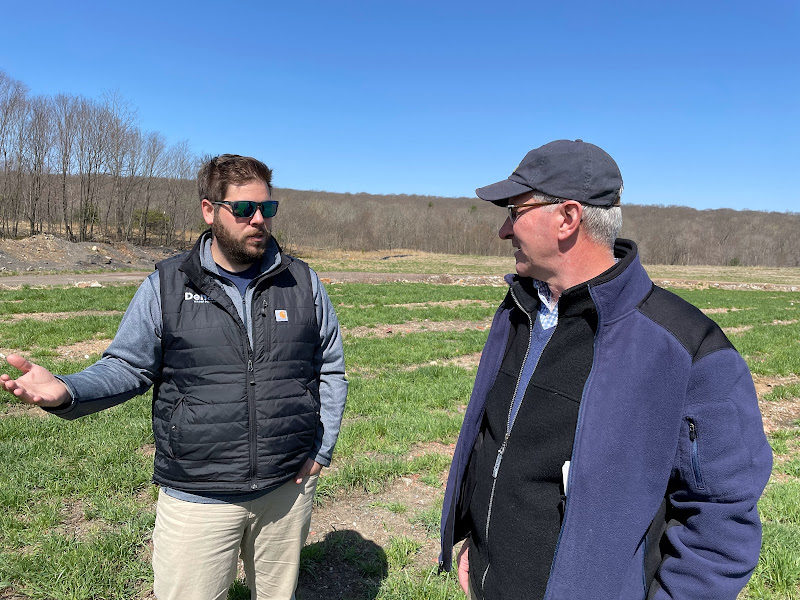
Ryan Chewinski conferring with a Denali colleague at a mine reclamation site in Pennsylvania
Ryan says of his work, “I may be delusional, but I believe our service to the farmers, my willingness to champion biosolids to any and everyone, gain public support. I talk about how we take a waste and turn moonscapes into meadows… it is a miracle.”
Mikayla Regan
Mikayla’s enthusiasm for her work at Northern Lancaster County Authority is clear and palpable. Her LinkedIn profile proclaims: “I am a dedicated and passionate water and wastewater professional.” That is very clear.
If Mikayla’s energetic enthusiasm for our profession evokes an image of a team of kids playing field hockey, well that is because field hockey coaching is very nearly a second career. Ice hockey is close to field hockey as a favorite sport.
Mikayla is a proud graduate of Thaddeus Stevens College of Technology in Lancaster, Pennsylvania. While attending the two-year Water and Environmental Technology program, she worked full-time as a drinking water operator at Red Lion Municipal Authority’s 3.5 MGD treatment facility. Her combined experiences prepared her to join Arro Consulting in the position of a circuit rider for a diverse caseload of different small to medium drinking water and/or wastewater treatment facilities spanning over 15 counties in the state. In this role, she saw and did it all – carrying out day-to-day operations, ordering chemicals and supplies, providing preventative maintenance, testing influent and effluent, responding to inclement weather, carrying out PA OneCalls, installing and reading meters and conducting inspections with DEP.
This expansive role could not contain Mikayla. She entered the consultant side of the profession with Material Matters in Elizabethtown, PA, a firm specializing in optimizing residuals treatment and utilization. With the support of her mentors, Mikayla emboldened her interest and involvement in the beneficial use of biosolids. And then she made her move to Northern Lancaster County Authority in Denver, Pennsylvania, a utility with an average daily flow of 400,000 gallons, where she now joins a team of 4 operators, one office administrator, and, in her words, “a great board.”
Northern Lancaster merges Mikayla’s wastewater and operations skills with her coaching skills. She helps train new operators and is the point person for the internship program with Thaddeus Stevens. She helps lead the biosolids beneficial use program, focusing on continued improvement, proactivity, and resiliency. In addition, Mikayla leads plant tours and is happy to spearhead a new internship program with her alma mater, Thaddeus Stevens. She hopes to help develop a stronger workforce, to emphasize the importance of beneficial use, and to encourage new operators. She also draws upon her communications skills to reach out to the public on environmental issues of the day, such as PFAS, and solicits public support for reducing nuisances that flows in the influent from the authority’s large waste watershed items such as rags, fibers wipes, personal waste items and persistent pollutants.
Mikayla is very mindful, too, as a lifelong resident of central Pennsylvania, of the virtues of frugality and self-reliance. She did not shy away from challenging the recommendation by the Authority’s engineer to landfill over 1,000 wet tons of biosolids in lieu of beneficial use for this summer’s reed bed excavation project. Northern Lancaster utilizes four reed beds to dewater aerobically digested solids and produces Class B biosolids. Each bed has 10 cells that are 25 feet by 50 feet in dimension and 6 feet in depth. All but one of the beds has had their original aggregate and sand media replaced with crushed, recycled glass. Recognizing the increasing challenges and expenses of small facilities faced with landfill disposal while keeping in mind concerns over PFAS, Mikayla successfully advocated for the Authority to screen their influent, effluent, biosolids, and reed trimmings for PFAS, and to continue to pursue beneficial use where applicable. The current enthusiasm for PFAS has the staff sampling each of the beds in turn, to establish whether the existing media and the reeds that grow in it can be recycled to land, or, instead, the media needs to be taken to be disposed of due to contamination. Annually, Northern Lancaster produces up to 100 dry tons of residuals for stabilization in the beds, where time and reed growth has resulted in a cakey, soil-like material infused with dry reeds. Sampling of the reed bed solids has demonstrated biosolids quality is suitable for mine reclamation.
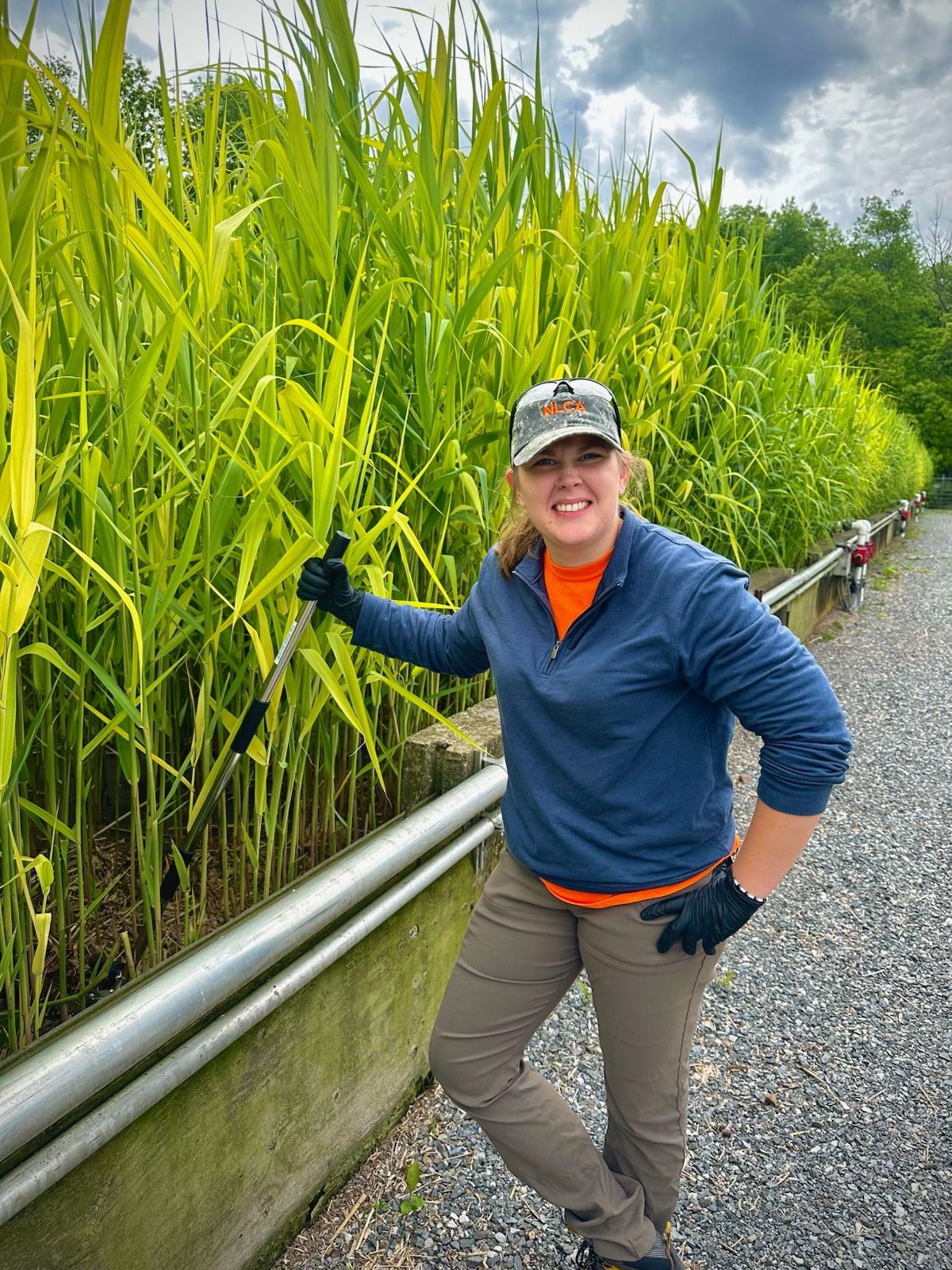
Mikayla Regan is holding a tool unofficially called the “poop scoop” which is used for inspecting reed bed loading and growth at the Northern Lancaster County Authority plant in Denver, Pennsylvania.
Mikayla speaks enthusiastically about her role as a champion of clean water to her customers. She is eager to face the PFAS issue head on, and she has made the case with her colleagues at small plants across the state that they should be in communication with customers on the issue of “forever chemicals,” in part because unreasonable fears may cause the public to insist on expensive agency actions.
If you want to catch Mikayla’s energy, she invites folks to seek her out at the MABA Summer Symposium, July 8 through 10th in Camp Hill, Pennsylvania.
Danielle Sheahan
“You ought to be an engineer,” Danielle Sheahan’s science teacher advised her as a Junior high student. Her first thought was railroading, of course, but this laid-back science teacher, retired from Anheuser-Busch who had turned to teaching for fun at Danielle’s Missouri high school, got his point across. When she landed at Missouri Science and Tech College, she flipped through the engineering majors, and environmental engineering jumped out at her, perhaps in part because this major had the fewest number of students. But from her very first class; she liked what she heard, and she heard a lot about wastewater and biosolids. The environmental program at this technical college included assisting wastewater research, and in Danielle’s case this included characterizing extracellular polymeric substances in laboratory reactors. Her college internship experience included modeling combined sewer overflows for a midWest city, participating in a conceptual master plan for a California utility, and developing safety protocols for a BeyondZero safety team.
Now a dozen years since she started environmental engineering, Danielle can say with enthusiasm, “Anaerobic digesters are cool, really cool!” And, indeed, Danielle is steeped at this moment on authoring a technical memorandum on digester cover performance for a client she will not name. Soon, she will be turning her sights on a digester system owned by a Utah agency that is considering refurbishment.
Brown & Caldwell was Danielle’s first employer out of college seven years ago, though she had an internship with Jacob in her last year of college. She works from home in Germantown, Maryland, in a national team at Brown & Caldwell that provides design services for the company. As Process Mechanical Engineer, Danielle gets to work on projects in all corners of the United States, for whatever component of wastewater her skills are needed. One project was a digester project in the South, and a second was a biosolids dryer project in New England. She also has had the fun of being part of a team bringing the EcoRemedy gasifier system to the Derry Township Municipal Authority in Hershey, Pennsylvania. She has had a key role in the design of pumps and conveyors; she will be watching to see if her designs for a cooling conveyor will be needed.
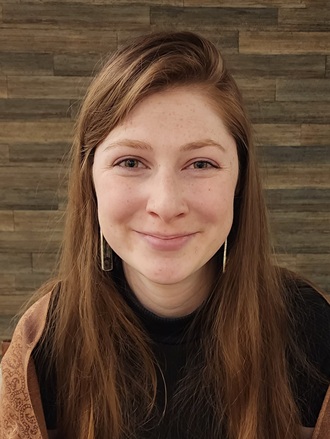
Danielle Sheahan taking a pause between digester design projects for Brown & Caldwell
The home office work suits Danielle. She met her future husband at a professional conference in Missouri, but his job took him to Washington, DC, so it was convenient to relocate. With a firm as broadly based as Brown & Caldwell, Danielle can turn to mentors such as Ted Hull in Atlanta and Tom Chapman in California.
We at the Mid Atlantic Biosolids Association can expect to hear from Danielle in the future, and not only because of her enthusiasm for wastewater and digestion. While still a student in Missouri Danielle completed the Competent Leadership program offered by Jacobs P3 Toastmasters Club.
Xiao Guo
“I like building things, that has been a consistent theme in my life. I even assembled my own PC, because I wanted to understand how the components worked together.” Xiao is eight years out of completing her engineering degree at the University of Delaware. Over these few years, first with Hazen and now with Carollo, Xiao has evolved into a professional engineer with a specialization in biosolids processes, including design of digesters, dewatering equipment, conveyors and cake storage. She is very close now to seeing a project from design concept all the way to installation: “it will be extremely satisfying to watch it come to life.”
Now 30 years old and living in the District of Columbia, Xiao was raised in suburban Boston with her brother. Xiao is proud of the high standard for hard work set by her mother, who had emigrated from China to attend college at the University of Georgia and who from there followed a steady professional trajectory from bank teller to a bank vice president. Xiao credits Delaware’s environmental engineering program for exceptional preparation, particularly in preparing her for the professional engineering exam. She also credits her career to great mentorship from some of the top biosolids engineers in the region, names familiar to the MABA community, such as Rashi Gupta, Paul Bassette, Matt Van Horne, and Paul Knowles.
Her enthusiasm for creating big things in biosolids was cemented by her early assignment to participate in the significant wastewater design projects. One of her first projects was the expansion of dewatering and thickening processes using centrifuges, where she was able to learn the design process from start to finish. She was then on a team that implemented a new chopper pump and jet mixing system for digesters for a plant located in Suffolk, VA. She recently completed a comprehensive review of digester mixing technologies for a California agency, which is currently in design, and has made recent professional presentations on that work.
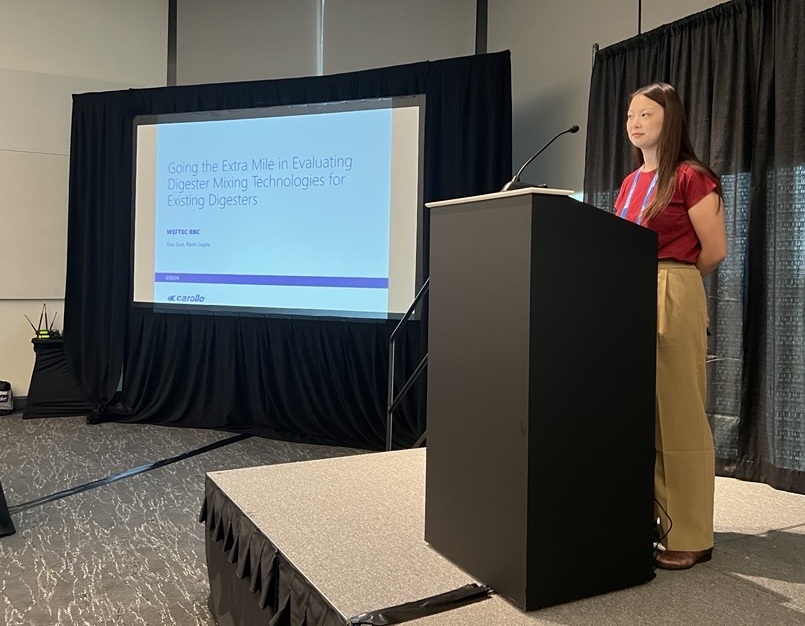
Xiao Guo is presenting on the variety of mixing pump technologies for anaerobic digesters on a project for a California agency with Carollo Engineers.
Xiao is primarily concerned with PFAS and microplastics in our water, and is interested in viable approaches to treat these pollutants. She is particularly interested in how we can use microorganisms to degrade plastics, similar to how we use microorganisms to remove pollutants like nitrogen from wastewater now. But when speaking with people of her generation, she can get frustrated by an apparent disconnect between environmental issues and water infrastructure. “They definitely have a passion for solving environmental issues and making the world a better place for future generations. But I feel there is a connection to critical infrastructure and its role in public health that is missing. We need to reach the young people and get them interested in using their talents to make and maintain clean water.”
To balance her inherited tendency to be a workaholic, Xiao turns to several activities. She has been a long-standing video gamer and keeps her Nintendo Switch console close at hand. Having taken art lessons as a child, at first reluctantly at her mother’s suggestion, Xiao paints with oil and acrylics as an adult, an act of meditative value. Xiao also likes to watch documentaries and learn more about the world around her by traveling when she is able. Other smaller hobbies include doing her own nails, watching movies, and enjoying time with friends. Another downtime activity is watching D-I-Y videos, which Xiao regularly marks for future reference for when she has a home of her own. After all, Xiao loves knowing how to create things, things as small as a painting and things as big as a wastewater plant. That is precisely the kind of engineer we all need in our biosolids profession.
For more information, contact Mary Baker at [email protected] or 845-901-7905. |
|