November 2024 - MABA Biosolids Spotlight
Provided to MABA members by Bill Toffey, Effluential Synergies, LLC
SPOTLIGHT on Piscataway Bioenergy Plant
When WSSC Water’s Theon Grojean was introduced at a construction industry seminar in 2017 to an “alternative delivery system” for public works projects, one message he heard from the dais was this: “if you are starting on your first Progressive Design-Build (PBD) project, start small.” But there was nothing small about what WSSC Water was looking at; it was nothing short of a total reconstruction of solids handling, affecting all of its WRRFs, the largest capital project in agency history. As Grojean and his bosses saw the project, everything about solids handling would change – stabilization processes would be moved to a centralized facility, its long-standing lime stabilization processes would be ended due to risks of community odor complaints; and anaerobic digestion would be introduced to reduce solids and capture energy. These plans for solids were also following on the heels of WSSC Water’s upgrade to liquid treatment with enhanced nutrient removal, a process that would inherently change solids dewaterability in the wrong direction.

The Piscataway Bioenergy Project is a regional facility handling solids from the Piscataway WRRF, WSSC Water’s largest plant at 30 MGD flow, and from 4 of the agency’s other facilities that together have a flow of about 65 MGD.
Yet, “PBD” had worked for DC Water in its half-billion-dollar biosolids project at Blue Plains, and that was encouraging to Grojean. The promise of PBD, as laid out by the Design-Build Institute of America, hit all the right notes. As DBIA asserts, PBD is “a highly collaborative, fully integrated undertaking that is built on trust, mutual respect, teamwork, innovation and creative problem solving.” If a project could benefit for collaboration and integration, the concept hatched for WSSC Water’s Piscataway plant in Accokeek, Maryland, was it. Jumping ahead 8 years, PBD was the mechanism of public infrastructure investment that has brought the Piscataway Bioenergy Project to the point of near completion.
The first step in PBD is the selection by WSSC Water of an “owner’s agent,” who could effectively watch for the agency’s interests in all stages of the complex processes -- planning, design, costing, bidding and constructing. WSSC Water selected HDR, Inc., a national comprehensive engineering firm with a strong presence in the mid-Atlantic and with a vice-president who had worked for many years on WSSC Water projects, Larry Hentz. Hentz, who for many years served on the MABA board of trustees, came to the role of owner’s agent with deep experience of the WSSC Water’s wastewater system, including being a lead on a biosolids master plan in 2005 that preceded the emergence of the centralization plan. Hentz thought he was heading toward retirement when the call came in 2018, but he has now seen the WSSC Water’s bioenergy project through to its near completion today. This project has been a good fit for Hentz’s interests, as he has helped guide other important and complicated biosolids projects, such as in Howard County and in Baltimore County.
The key step in PDB is selection of the firm that is the lead in coordinating design, engineering, and construction. This is a competitively bid contract, and for WSSC Water the firm PC Construction, out of Vermont, provided the best offer. PC Construction was not new to wastewater projects, with highly regarded projects in Fairfax and Prince Williams counties. Neither was it new to the Cambi Thermal Hydrolysis Process, a technology pre-selected and purchased by WSSC Water for solids pretreatment, as PC had been part of the DC Water project.
Important to WSSC Water was PC Construction’s selection of a design and engineering team with which WSSC Water was well acquainted – Stantec and Hazen and Sawyer. Matt Van Horne, associate vice president at Hazen, threw himself into the project, leaving his voluntary position on the MABA Board of Trustees to devote his full attention to the Piscataway project. Among the elements that provoked Van Horne’s early attention was the design of the digesters. As Piscataway is across the Potomac River from historic Mount Vernon, digesters were required to have a low profile, but poor foundation conditions and hydraulic issues prevented their deep placement. Rapid Volume Expansion within digesters can arise from a combination of rich feed and difficult mixing, posing a risk of overflows and spills. This concern led to several innovative design solutions, including a flume that would direct overflow from the digesters back to the headworks and a system to deliver emergency electricity to digester mixers in the event of plant power outage. Another design concern was in struvite control, an issue made salient by recent conversion of several WSSC Water’s plants to enhanced nutrient removal, which can cause phosphorus release during anaerobic digestion, leading to a risk of deposits throughout the digested solids and filtrate treatment systems. Several proprietary systems for handling struvite served as options for phosphorus extraction as a fertilizer or for phosphorus sequestration within the solids. The use of ferric chloride to sequester soluble P as a near term solution was the approach selected for Piscataway.
Piscataway has benefited from serendipity. WSSC Water embarked on its plans to replace odorous lime stabilization and to consider centralization prior to DC Water’s success at its Blue Plains plant with the Cambi Thermal Hydrolysis Process (THP). But with this nearby facility as a successful model, WSSC Water could have confidence in DC’s experience. WSSC Water’s team then extended that experience with visits to Cambi projects in Europe that included regional treatment of multiple solids sources, as WSSC Water was considering. Having selected THP, and having proceeded with its purchase in 2018, WSSC Water then managed to dodge the unforeseeable supply chain disruptions that later occurred during the covid pandemic, thus enjoying a serendipitous timing.
A second serendipity is the value of the biogas WSSC Water will be producing at Piscataway. The nation-wide value of renewable natural gas (RNG) derived from municipal digesters became more predictable and actionable as Piscataway planning proceeded. WSSC Water could count on revenue from selling its RNG to Montgomery County to help power about half of its fleet if natural gas Ride On buses and to the utility Washington Gas under the Renewable Fuel Standard Program.
A third serendipity is the value of the biosolids product WSSC Water will produce. With DC Water having invested substantial effort and time in its marketing of its Bloom biosolids product, WSSC Water will be using “lessons learned” with Bloom and the experience of DC’s marketing team at Blue Drop in designing a WSSC Water utilization program. Malcolm Taylor has been a fierce investigator into maximizing the quality of the biosolids and balancing those features with the potential customers. Taylor introduced his “Handleability Index” to help inform the targeted product users. WSSC Water has teamed up with Hazen and Material Matters, another key biosolids consultant and MABA member, to develop a marketing plan.
A fourth serendipity is emergence of approaches to ammonia removal from filtrate produced at the belt filter presses, a process known as “deammonification.” A potentially serious downside of centralized dewatering of anaerobically digested solids is high ammonia in return centrate from dewatering, making compliance with effluent nitrogen standards difficult to achieve. Systems deploying a class of bacteria known as “anammox” can convert ammonia to nitrogen gas with significantly less oxygen and supplemental carbon requirements, an approach which has come on the treatment scene in the past two decades and a process far more energy efficient than alternatives. WSSC Water is installing anammox treatment to keep ammonia return to the headworks within levels that enable the agency to attain nitrogen loadings assigned to its WRRFs in this very sensitive watershed of the Chesapeake Bay Watershed.
A fifth serendipity is with the status of WSSC Water’s project to the global evolving concern with the class of so-called “forever chemicals,” or per- and poly-fluoroalkyl substances (PFAS). While the EPA has not yet issued its evaluation of risks to human and environmental health from PFAS-bearing biosolids, WSSC Water believes that its current commitment to a high-quality, recyclable product at Piscataway is a sound one, nonetheless.
October 30 was the official grand opening for Piscataway Bioenergy Facility. The WSSC Water press release was titled “We’ve Got the Power! WSSC Water Celebrates Grand Opening of its Poop-to-Power Bioenergy Facility.” Congressmen, local elected officials and agency senior staff, as well as the MDE Secretary, joined in the ceremony. This marked the moment, according to the press release, when WSSC Water “officially opened its $271 million Piscataway Bioenergy Facility in Accokeek, Maryland. The innovative plant, which was completed on budget and on time, will turn “Poop to Power” by turning methane gas into Renewable Natural Gas (RNG) to power Montgomery County Ride On buses. …and [it] transforms how Maryland’s largest water utility handles biosolids…. Once fully operational in early 2025, all biosolids from WSSC Water’s five water resource recovery facilities (WRRFs) will be delivered to the new plant.”
Websites for Stantec and Hazen and Sawyer covered the significance of the project. Stantec’s article explains: “The facility is projected to generate approximately $4 million per year in revenue, save WSSC Water customers approximately $3.4 million per year in operating costs, and further reduce WSSC Water’s greenhouse gas emissions.” Hazen’s article explains: “The utility officially cut the ribbon on the $271 million bioenergy system on October 30…. This facility greatly reduces the amount of treated biosolids that need to be hauled away, which means fewer trucks and less fuel….” Hazen elaborates on the elements of the new biosolids treatment system:
-
cake silo storage for the Piscataway cake and bins for receiving raw solids from the 4 other WSSC Water plants;
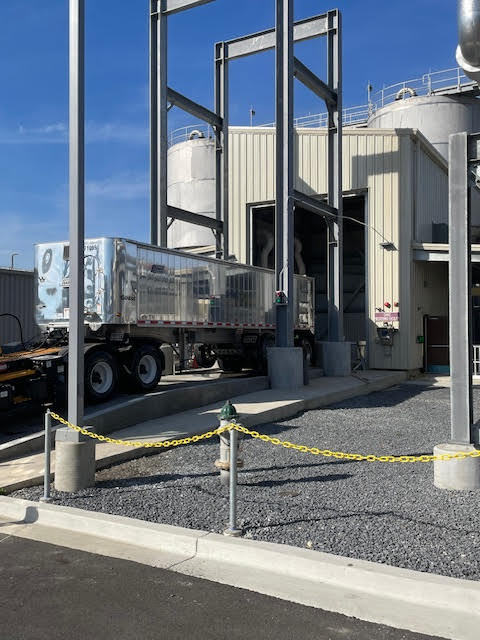
Piscataway Bioenergy will accept truck deliveries of dewatered raw solids from all plants for blending and feeding into stabilization equipment
2. the Cambi Thermal Hydrolysis Process (THP) system for pretreating solids for enhanced digestion;
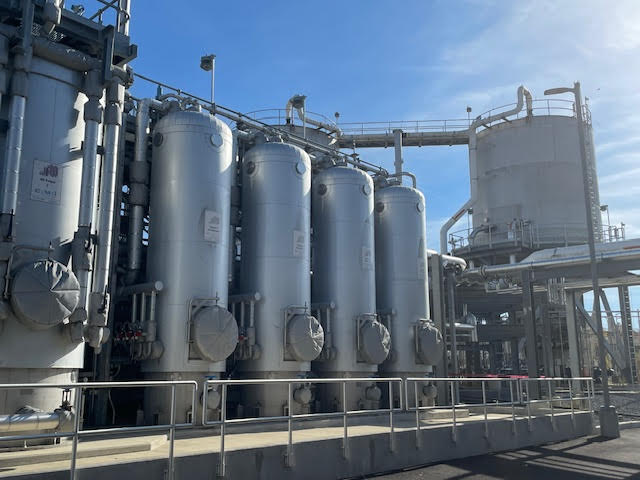
The Cambi Thermal Hydrolysis Process reactors, shown effective at DC Water’s Blue Plains plant, use high temperature and pressure steam to pretreat wastewater solids for high performance mesophilic anaerobic digestion.
3. steam generators and associated piping for supplying pressured steam to the THPs, designed to accept various fuels from biogas and natural gas sources;
4. cooling heat exchanger to reduce the temperature of the sludge feed ahead of mesophilic digestion;
5. two 1.5-million-gallon mesophilic anaerobic digesters;
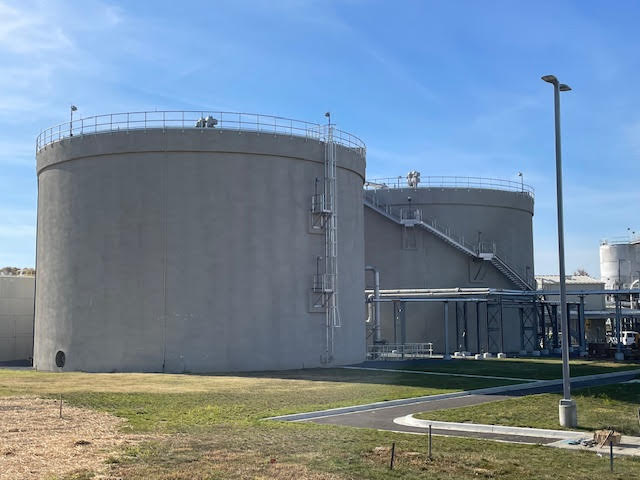
WSSC has built two conventional mesophilic digesters, each 1.5 million gallons in capacity, to digest the hydrolyzed wastewater solids, reducing organic matter by better than 50 percent, and converting it to biogas.
6. belt filter presses to dewater the class A solids;
7. gas storage to contain the biogas produced during volatile solids destruction for clean up to remove moisture, hydrogen sulfide, and carbon dioxide to produce Renewable Natural Gas (RNG);
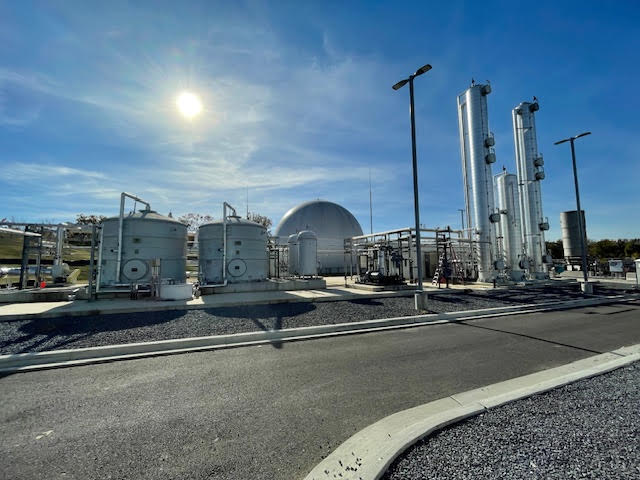
Biogas from digestion is upgraded to high value by removing moisture, CO2, siloxane and sulfur compounds, such that the final gas is equivalent to natural gas, but with an attribute as renewable natural gas that confers high economic value.
8. three 1.5 MW cogeneration engines to produce electricity from the RNG;
9. two anammox sidestream reactors for treating filtrate to remove ammonia prior to filtrate return to the head works;
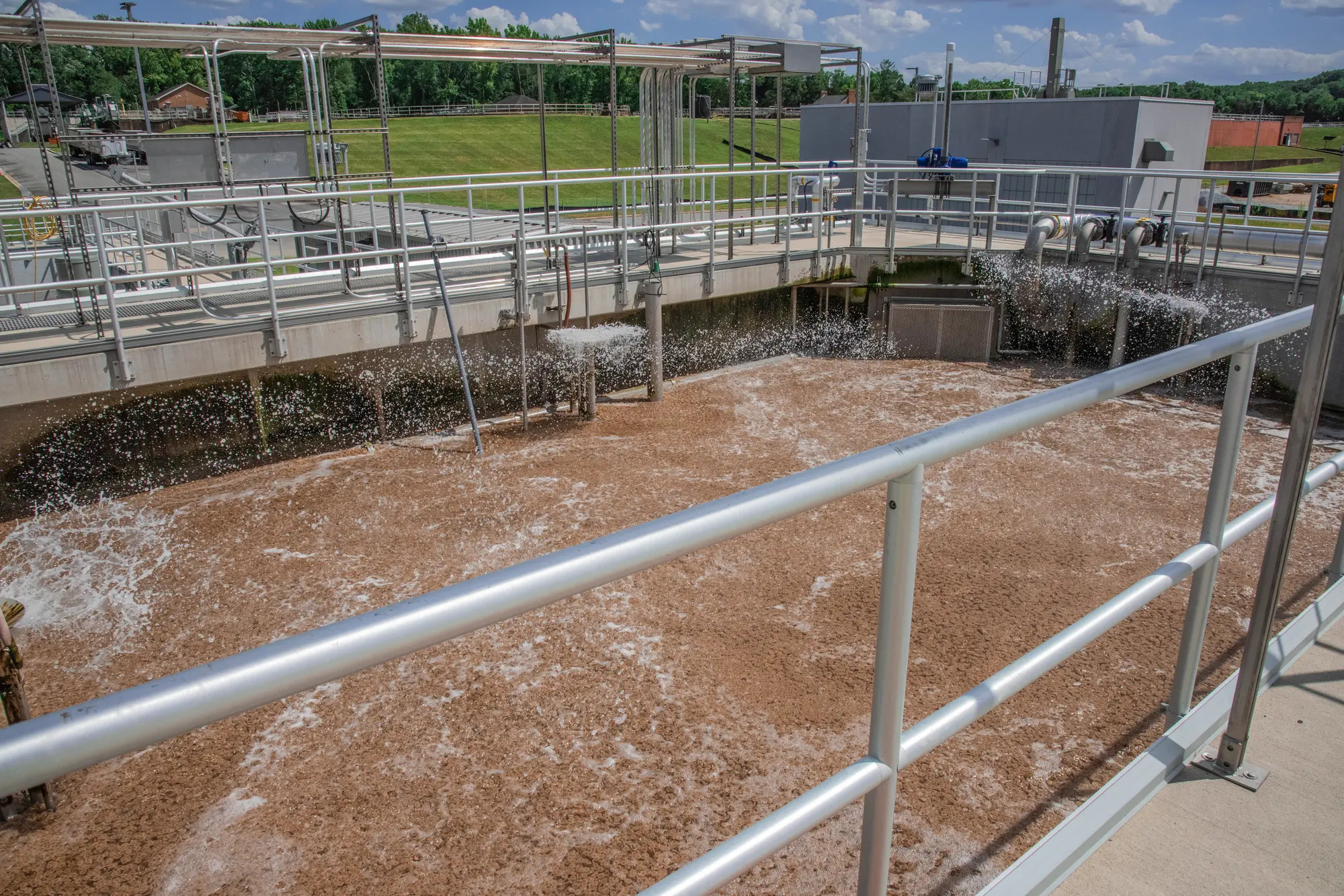
The sidestream treatment system uses a novel technique called deammonification that removes ammonia by using special bacteria grown on plastic media roughly the shape and size of wagon wheel pasta.
10. covered storage and a loading station from which the biosolids product is distributed.
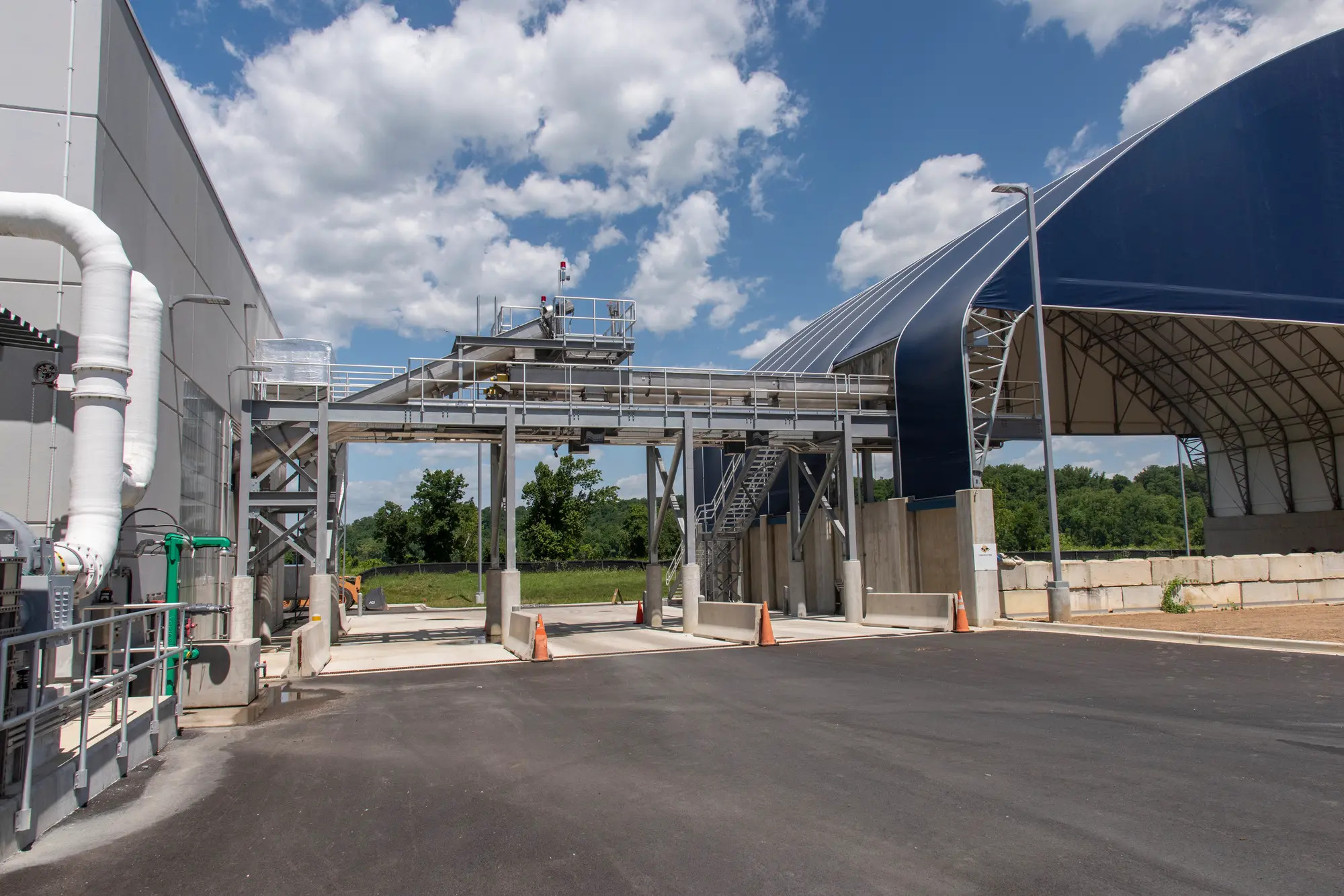
Class A biosolids are dewatered by belt filter presses to remove excess water and sent to this loading station or to the adjoining covered storage area.
Ever since the Piscataway team – WSSC Water, HDR, PC Construction and engineering firms Stantec and Hazen, together -- reached its 30% design mark back in 2018, a principal goal was to have Piscataway run dependably with WSSC Water’s own operators. At the center of this goal emerged Will Mapes, the Chief Plant Operator, Bioenergy Facility. Over the period 2018 to today, Mapes’s role at WSSC Water has expanded with the expansion of the facility. Mapes is particularly proud of the team of operators he has recruited. Mapes has had a special focus on effective screening of sludge feeds to the THP and digester of trash, fibers and grit, to avoid equipment downtime and maintenance time. He has been also a keen advocate for treatment that minimizes odors in the final biosolids product, to avoid site odors and to keep product moving to customers. Mapes brings these kinds of overarching goals to the systems he will be living with every day.
Supporting Mapes on the operability of Piscataway along the way has been Amanda Harris, the senior Commissioning Manager for PC Construction. She worked with PC Construction on Blue Plains as her first THP experience, and applied valuable lessons learned there to the WSSC Water project. When Piscataway is completed, Harris then will be taking on her third THP-MAD project, that of the facility planned for Arlington County Water Pollution Control Bureau. For Harris, Piscataway has been a “dream,” and she gave a shout out to the commitment of WSSC Water to ensuring the facility will be designed and built with operations staff top-of-mind. Her current challenges include bringing the innovative sidestream deammonification system fully online and completing the installation of the boiler for the Cambi THP. The boiler has been delayed by supply chain challenges but also by the requirement that it take all types of fuels in addition to RNG, including surplus biogas and exhaust from the generators.
WSSC Water’s Piscataway Bioenergy Facility is very, very close to completion. Over the next several months, solids from the outlying WRRFs are introduced to the receiving station, thereby expanding the volume of solids flowing through all components of the treatment train. Now that a final dewatered digested cake is in production at Piscataway the very significant “what’s next” for distribution of the dewatered cake is center stage. 2025 will be the year in which all parts of the dream, which took shape in 2018, are in place.
Congratulations to this amazing team.
For more information, contact Mary Baker at [email protected] or 845-901-7905. |